Bohrwerk Machine Tools Inspection
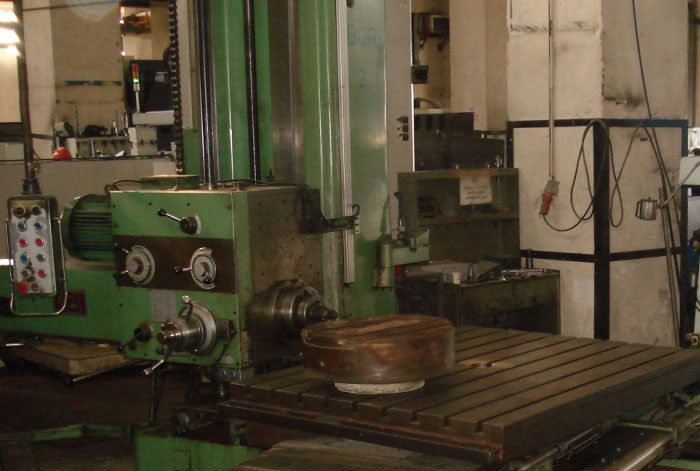
Bohrwerk machines are used for machining workpieces that are too large and heavy to be machined on milling machines. These machines are horizontal boring machines, but are commonly known as Bohrwerk machines. In the German language, the word bohrwerke means boring, catheter, and this name has entered the German language.
Bohrwerk benches or horizontal boring benches are generally used for boring, enlarging and similar operations. Even very long holes can be machined with precision and quality.
In this type of machine, as in milling machines, multi-point cutting tools as well as single-end cutting tools can be used. These cutting tools are also the same types used in CNC machining centers. The universal head can be connected to the spindle of Bohrwerk machine tools to perform operations at different angles and positions. The table to which the workpieces are connected is capable of both linear movement and 360 rotation about its axis. In this way, it is possible to treat each surface of the workpieces.
In fact, as with all machine tools, Bohrwerk machines are among the machines and equipment that pose a danger to the health of employees and the safety of employers. As such, periodic checks of Bohrwerk machine tools must be carried out in accordance with the provisions of the Regulation on Health and Safety in the Use of Work Equipment.
During the control procedures in the authorized test and inspection institutions, the relevant standards are followed firstly, and if there is no time or condition specified in these standards, the time and conditions deemed appropriate by the companies producing these machines are followed. If there is no prediction in the manufacturer companies, a risk assessment study is conducted and control periods and control criteria are determined according to the results. Factors such as operating conditions, frequency and duration of use of these machines are taken into consideration in the risk assessment study. However, the control period to be calculated must not exceed one year.
Our company, Bohrwerk machine tools inspection, in accordance with the relevant legal regulations, standards and test methods published by domestic and foreign organizations. In this regard, our company, the Turkish Accreditation Agency (TÜRKAK), It is accredited in accordance with TS EN ISO / IEC 17025 standard. In this way, the control and inspection procedures and reports issued are deemed valid for private and official audits.