Radiographic Examination (RT)
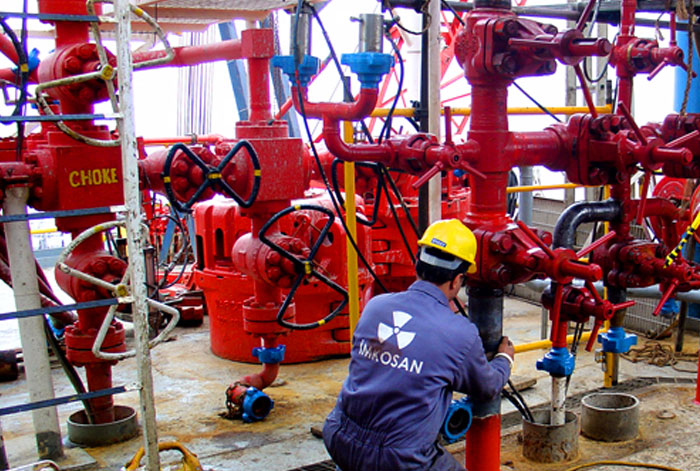
Radiographic testing (RT) is also known as industrial X-ray method. In this method, electromagnetic radiation of short wavelength is applied to the material to find hidden defects in the material. That is, high energy photons are sent into the material. This non-destructive testing method, which is frequently applied in the industry, uses an X-ray machine or a radioactive source.
A similar method is the neutron radiological test method. Neutrons are used in this method instead of photons. This method is preferred because neutrons can easily pass through lead and steel, but are retained by water, oil or plastic. Using X-rays, the details in the material are clearly revealed.
In the radiographic examination method, the amount of radiation emitted behind the material is measured. By evaluating changes in radiation intensity, information is obtained about the thickness of the material or the composition of the material.
Radiographic examination is a highly sensitive method and the results of the examination can be recorded permanently. Therefore, it is widely used in industry.
When high-energy electromagnetic waves penetrate the material, the internal image of the material through which the radiation passes through the radiation-sensitive films on the other side of the material appears. This image is caused by gaps or density changes in the material. This method can be applied to all materials, both metal and non-metal.
Our company is non-destructive also provides radiographic examination services within the framework of inspection services. In these studies, relevant legal regulations, standards and test methods published by local and foreign organizations are complied with. A few standards are based on:
- TS EN ISO 5817 Welding - Steel, nickel, titanium and their alloys melting welded (not including bundle welding) - Quality levels for defects)
- TS EN ISO 5579 Non-destructive testing - Radiographic examination of metallic materials by film and X or gamma rays - General rules
- TS EN ISO 17636-1 Non-destructive testing of weld seams - Radiographic inspection - Part 1: Film X and gamma ray techniques
- TS EN 12681 Castings - Radiographic examination
- TS EN ISO 10675-1 Non-destructive testing of welds - Acceptance levels for radiographic examination - Part 1: Steel, nickel, titanium and their alloys
- TS EN ISO 17635 Non-destructive testing of welds - General requirements for metallic materials